

During the soldering process, different issues may occur leading to the inception of some defects (tombstone effect, flux spattering, etc.). The most common technique of soldering used in electronics is the reflow soldering. One of the most vulnerable components of electronic circuits is the solder joints. It does not however, greatly impact key metallurgical properties such as intermetallic layer thickness. The results demonstrated that reflow profile affects properties such as metal wetting and voiding. After analysis, the PCBs were then subjected to thermal cycling experiments to see how reflow profile impacted microstructure evolution. The PCBs were then analyzed to see how the processing variables influenced wetting, voiding, microstructure, intermetallic layer composition, and thickness. Each alloy was processed using different reflow profiles that had varying times above liquidus (TALs) and peak temperatures. The following study looks at the behavior of four different Sn–Bi alloys-traditional 42Sn58Bi and 42Sn57Bi1Ag and two new tin–bismuth alloys-in solder paste during the reflow soldering process. While certain tin–bismuth solders are well characterized many new alloys in this family have been developed which need proper characterization.

Sn–Bi alloys are desirable candidates for soldering components on printed circuit boards (PCBs) because of their low melting point and reduced cost. The hybrid physics–ML model providing accurate prediction with the significantly reduced expense is used in this application for the first time. This study provides a smart solution to determine the optimal preset temperatures of the reflow oven, which is usually relied on experience. The study of reflowing a new PCB assembly can be started at the early stage of board design with no need for a physical profiling board prototype. The prediction of the reflow profile subjected to varied temperature settings of the reflow oven is beneficial to process engineers when reflowing bulky components. Using this system, the reflow oven temperature settings to achieve the desired reflow profile can be obtained at substantially reduced computation cost. Integrated physical and ML models synergistically can accurately predict reflow profiles of solder joints and alleviate the expense of repeated trials.
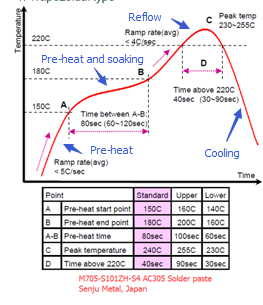
Support vector regression and an artificial neural network are used to validate the accuracy of ML models. The training data provided to the machine learning (ML) model is generated from a programmed system based on the physics model. In this study, computational fluid dynamics modeling is used to simulate the reflow soldering process. This paper aims to provide the proper preset temperatures of the convection reflow oven when reflowing a printed circuit board (PCB) assembly with varied sizes of components simultaneously. No significant difference was found between the used solder masks therefore, it is possible to use the novel, directly printed one without increasing the risk of flux spattering. The type of solder pad design also slightly affected the flux spattering. Changing the flux from ROL1 to ROL0 reduced the flux spot occurrence by 62 % on average. The results showed a strong influence of flux chemistry on spattering. The testing board included real-sized soldering pads and a boron-silicate glass slide as a target area, ensuring the same evaluation process for all samples. A unique design of the test board was developed for a proper evaluation of flux spatter spots spattered from the solder paste. Several factors entering the process were investigated: the type of flux in the solder paste (ROL0/ROL1 according to the IPC J-STD-004B standard), the type of solder mask (liquid photo imageable/directly printed), and the type of solder pad design (copper-defined/solder mask-defined). This comprehensive study dealt with the reliability issue of no-clean flux spattering from the solder paste during the reflow soldering process.
